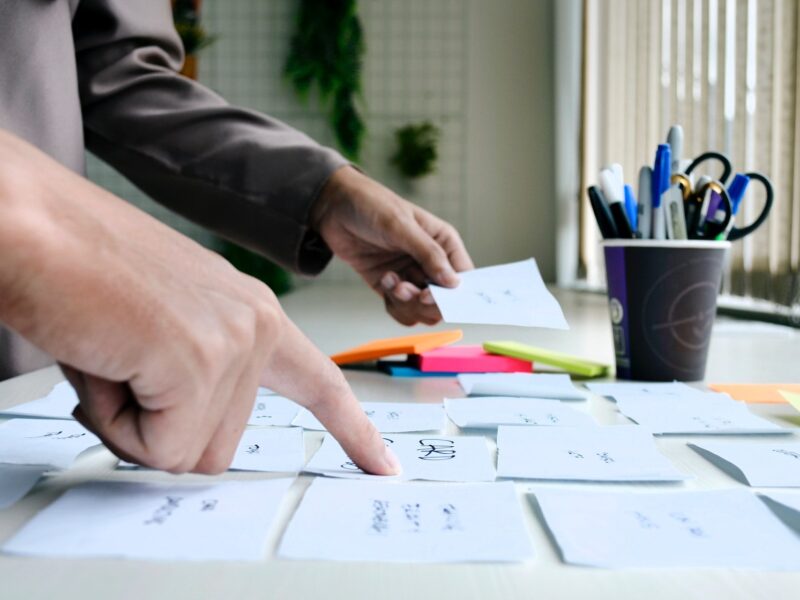
Choosing the Right Plastic Material for Your Product: A Guide for Entrepreneurs
Selecting the right plastic material is a crucial decision for entrepreneurs looking to manufacture products using injection moulding. The right material impacts product durability, cost, aesthetics, and functionality. This guide will help you understand the key factors to consider and how to choose the best plastic for your specific application.
Key Factors to Consider When Choosing a Plastic Material
- Strength & Durability
- If your product requires high mechanical strength, opt for materials like ABS, Polycarbonate (PC), or Nylon.
- For softer, impact-resistant items, Polypropylene (PP) or TPU (Thermoplastic Polyurethane) can be ideal.
- Heat Resistance
- Products exposed to high temperatures should use Polyetheretherketone (PEEK), Polycarbonate (PC), or PPS (Polyphenylene Sulfide).
- Everyday applications requiring moderate heat resistance can use ABS or PET (Polyethylene Terephthalate).
- Flexibility & Elasticity
- For bendable and stretchable parts, TPU, Silicone, or Polyethylene (PE) are excellent choices.
- Polypropylene (PP) also provides flexibility while maintaining durability.
- Chemical & Corrosion Resistance
- For medical, food-grade, or chemical applications, HDPE (High-Density Polyethylene), PEEK, or Teflon (PTFE) offer high resistance to solvents and corrosion.
- Polypropylene (PP) is commonly used in food containers and medical products due to its resistance to moisture and chemicals.
- Transparency & Aesthetics
- If your product requires transparency, consider Polycarbonate (PC), Acrylic (PMMA), or PET.
- For high-gloss finishes, Polystyrene (PS) or ABS work well.
- Cost & Production Efficiency
- Polypropylene (PP) and Polystyrene (PS) are cost-effective and widely used in mass production.
- For premium applications, Polycarbonate (PC) and PEEK are durable but more expensive.
Common Plastic Materials & Their Applications
Plastic Type | Key Properties | Common Applications |
ABS (Acrylonitrile Butadiene Styrene) | Strong, impact-resistant, heat-resistant | Automotive parts, consumer electronics, tool housings |
Polypropylene (PP) | Flexible, chemical-resistant, lightweight | Food containers, medical devices, packaging |
Polyethylene (PE) | High strength, moisture-resistant, affordable | Bottles, bags, pipes |
Polycarbonate (PC) | High impact resistance, transparent, heat-resistant | Safety goggles, automotive headlights, electronics casings |
Nylon (Polyamide) | Strong, wear-resistant, flexible | Mechanical gears, bearings, textiles |
PET (Polyethylene Terephthalate) | Transparent, food-safe, strong | Water bottles, food containers, packaging |
PEEK (Polyetheretherketone) | High-temperature resistant, strong, chemical-resistant | Medical implants, aerospace components, high-end mechanical parts |
Steps to Choose the Best Plastic for Your Product
- Define Product Requirements
- Consider durability, environmental conditions, load-bearing capacity, and chemical exposure.
- Evaluate Cost vs. Performance
- Balance cost-effectiveness with required performance and longevity.
- Consider Manufacturing Efficiency
- Some plastics are easier to mould than others, affecting production speed and quality.
- Test with Prototyping
- Before full production, use 3D printing or small-batch injection moulding to test different materials.
- Consult with Experts
- Work with plastic manufacturers or material engineers to ensure the right material choice for your specific needs.
Final Thoughts
Choosing the right plastic material can significantly impact the quality, cost, and functionality of your product. Entrepreneurs should assess their product’s specific needs and test materials before mass production.
At Injection Moulding Works, we help businesses select the best plastic for their manufacturing needs, ensuring optimal performance and cost-efficiency. Contact us today for expert guidance and customised solutions!